Get consistent results with skilled plastic extrusion techniques
Get consistent results with skilled plastic extrusion techniques
Blog Article
A Comprehensive Guide to the Process and Advantages of Plastic Extrusion
In the huge world of manufacturing, plastic extrusion becomes a highly effective and vital process. Translating raw plastic into constant accounts, it satisfies a plethora of markets with its impressive versatility. This guide aims to elucidate the intricate steps associated with this method, the kinds of plastic proper for extrusion, and the game-changing advantages it gives the market. The following conversation guarantees to unfold the real-world influences of this transformative process.
Recognizing the Essentials of Plastic Extrusion
While it may show up complex in the beginning glimpse, the process of plastic extrusion is basically simple - plastic extrusion. It is a high-volume manufacturing technique in which raw plastic is melted and formed into a continuous profile. The process starts with the feeding of plastic product, in the type of powders, granules, or pellets, into a heated barrel. The plastic is then melted using a combination of heat and shear, used by a revolving screw. When the molten plastic gets to the end of the barrel, it is required with a small opening called a die, shaping it right into a preferred kind. The designed plastic is then cooled down, solidified, and reduced into desired lengths, finishing the process.
The Technical Process of Plastic Extrusion Explained
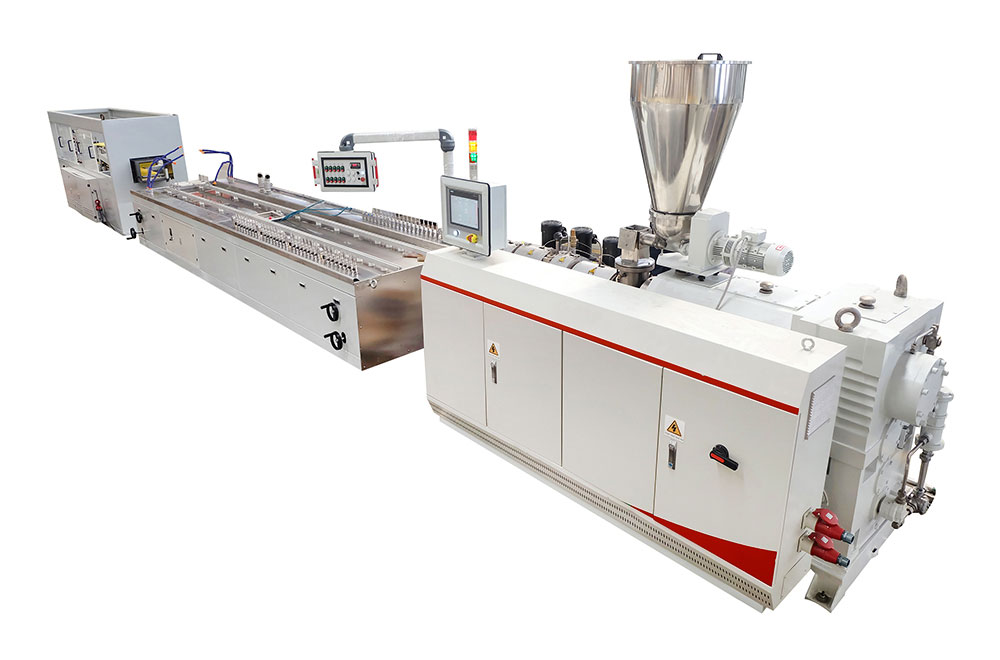
Sorts Of Plastic Suitable for Extrusion
The choice of the appropriate type of plastic is an important facet of the extrusion procedure. Numerous plastics provide distinct properties, making them extra matched to specific applications. Understanding these plastic kinds can substantially enhance the extrusion procedure.
Comparing Plastic Extrusion to Various Other Plastic Forming Techniques
Recognizing the sorts of plastic appropriate for extrusion leads the means for a wider conversation on how plastic extrusion stacks up against various other plastic developing methods. These consist of injection molding, blow molding, and thermoforming. Each approach has its unique usages and benefits. Shot molding, for example, is excellent for developing intricate components, while impact molding is excellent for hollow items like bottles. Thermoforming excels at developing superficial or big components. Plastic extrusion is unmatched when it comes to developing continual accounts, such as seals, pipes, and gaskets. It also permits a consistent cross-section along the length of the item. Thus, the selection of approach mostly relies on the end-product demands and specifications.
Key Benefits of Plastic Extrusion in Manufacturing
In the realm of manufacturing, plastic extrusion supplies several substantial advantages. One noteworthy benefit is the cost-effectiveness of the process, that makes it an economically attractive manufacturing method. Furthermore, this technique offers superior product flexibility and boosted production speed, thereby enhancing total production effectiveness.
Affordable Production Technique
Plastic extrusion leaps to the forefront as an economical production method in production. In addition, plastic extrusion needs much less energy than typical manufacturing methods, adding to reduced operational prices. In general, the financial benefits make plastic extrusion an extremely appealing choice in the manufacturing market.

Superior Item Versatility
Past the cost-effectiveness of plastic extrusion, an additional significant benefit in making lies in its premium product versatility. This procedure enables the development of a vast range of products with varying dimensions, styles, and shapes, from easy plastic sheets to detailed accounts. The flexibility is attributed to the extrusion die, which can be tailored to generate the desired product design. This makes plastic extrusion an optimal service for markets that require customized plastic parts, such as auto, building and construction, and packaging. The capacity to produce varied items is not just valuable in meeting certain market needs however additionally in enabling makers to explore new line of product with very little capital expense. click to find out more In significance, plastic extrusion's product flexibility promotes technology while improving functional effectiveness.
Improved Production Speed
A considerable benefit of plastic extrusion lies in its improved manufacturing speed. Couple of other manufacturing procedures can match the rate of plastic extrusion. In addition, the capacity to preserve regular high-speed production without compromising product top quality sets plastic extrusion apart from various other methods.
Real-world Applications and Effects of Plastic Extrusion
In the world of manufacturing, the technique of plastic extrusion holds extensive importance. This process is widely used in the production of a range of products, such as plastic tubes, home window frameworks, and weather removing. Because of this, it considerably affects markets like building and construction, product packaging, and auto markets. Its effect expands to day-to-day products, from plastic bags to toothbrushes and non reusable cutlery. The financial benefit of plastic extrusion, primarily its economical and high-volume output, has actually transformed manufacturing. The ecological effect of plastic waste stays an issue. The market is persistently striving for technologies in eco-friendly and recyclable products, showing a future where the advantages of plastic extrusion can be preserved without endangering ecological sustainability.
Final thought
In final thought, plastic extrusion is a effective and highly efficient approach of transforming basic materials into varied Learn More products. It supplies many advantages over other plastic developing approaches, consisting of cost-effectiveness, high outcome, you can look here very little waste, and layout versatility. Its effect is profoundly really felt in numerous sectors such as building and construction, automobile, and durable goods, making it a pivotal process in today's production landscape.
Delving deeper right into the technical procedure of plastic extrusion, it begins with the selection of the suitable plastic material. When cooled down, the plastic is reduced into the called for sizes or wound onto reels if the product is a plastic movie or sheet - plastic extrusion. Comparing Plastic Extrusion to Other Plastic Forming Techniques
Comprehending the types of plastic suitable for extrusion paves the way for a more comprehensive discussion on how plastic extrusion stacks up versus various other plastic forming methods. Few various other manufacturing processes can match the speed of plastic extrusion.
Report this page